We were recently award a Critical Technologies grant to perform a feasibility study integrating 3D printing, 3D scanning, and commercially available optically pumped magnetometers (OPMs) to develop a low-cost, modular brain imaging system. The study leverages 3D scanning to generate accurate anatomical models of individual subjects’ heads, which are then used to fabricate custom-fit OPM sensor mounts via high-resolution 3D printing.
This tailored approach ensures optimal sensor-to-scalp proximity and alignment, which is critical for detecting the femtotesla-scale magnetic fields generated by neural activity. Using off-the-shelf OPMs operating in the spin-exchange relaxation-free (SERF) regime, we assessed the signal-to-noise ratio and spatial resolution achievable with this configuration through phantom testing and computational modelling. Our findings demonstrate that with precise sensor placement and adequate magnetic shielding, this platform can resolve cortical activity patterns, suggesting a viable pathway toward portable, cost-effective brain imaging for clinical and research applications.
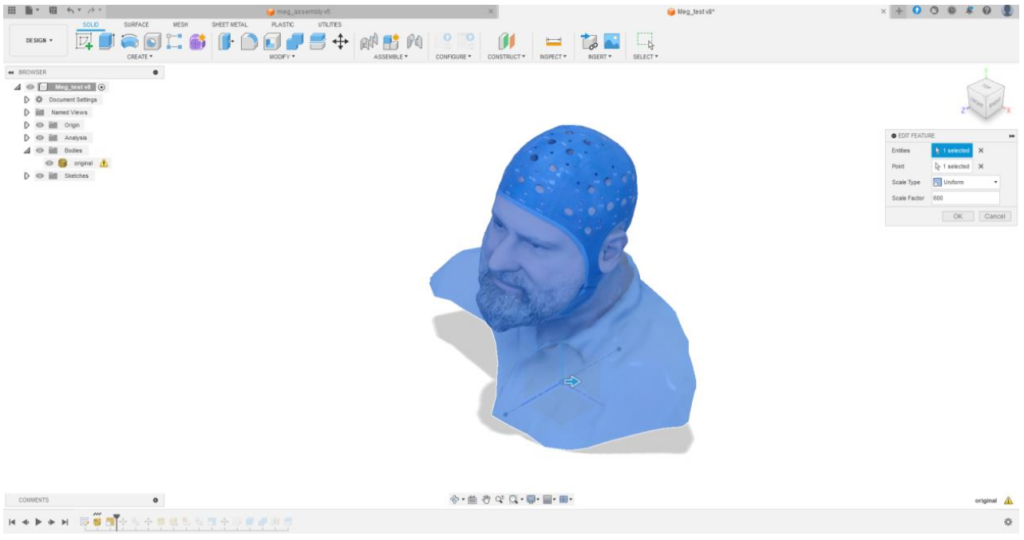
The following hearing aid study focuses on the development and impact of fashionable, customised hearing aids designed specifically to enhance acceptance and usage among young users. By integrating advanced 3D printing technologies and user-centric design principles, we created hearing aids that are both functionally sophisticated and visually appealing, offering personalisation in colour, shape, and style.
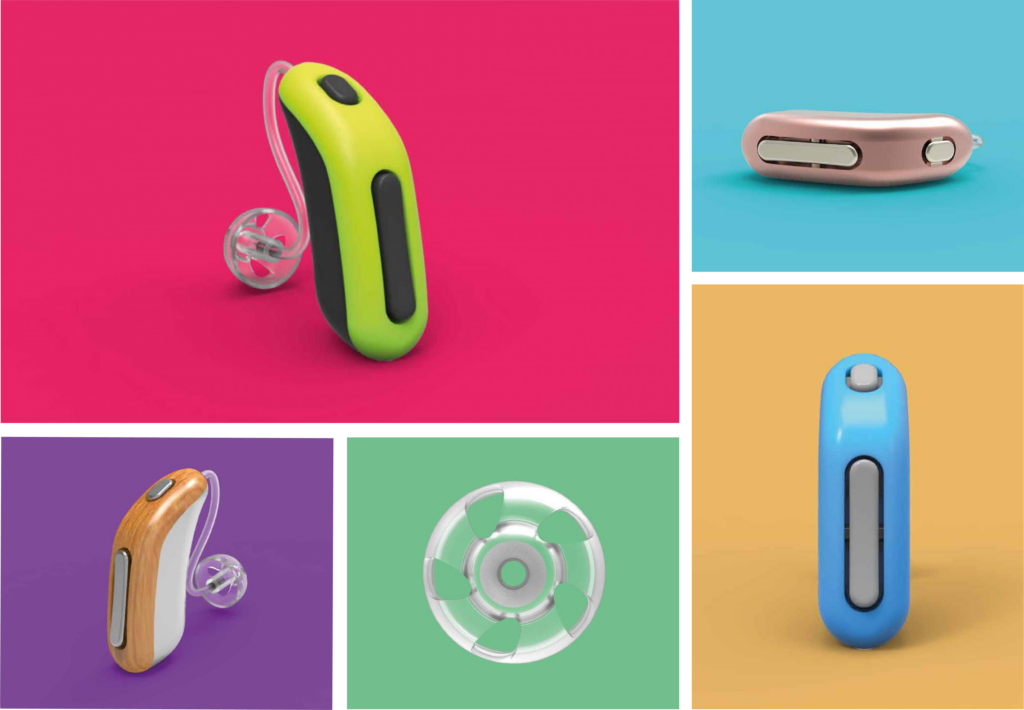
The feedback we received from our designs indicate that aesthetic customisation may significantly reduce stigma associated with hearing aid use, particularly among adolescents and young adults, who are often sensitive to peer perception. Additionally, personalized designs encourage consistent device usage, improving auditory outcomes and overall quality of life.
The integration of modern materials and low-profile components also enables enhanced comfort and acoustic performance without compromising style. These findings support a multidisciplinary approach—blending audiology, industrial design, and psychosocial research—to improve device adherence and redefine hearing aids as wearable technology rather than medical appliances.
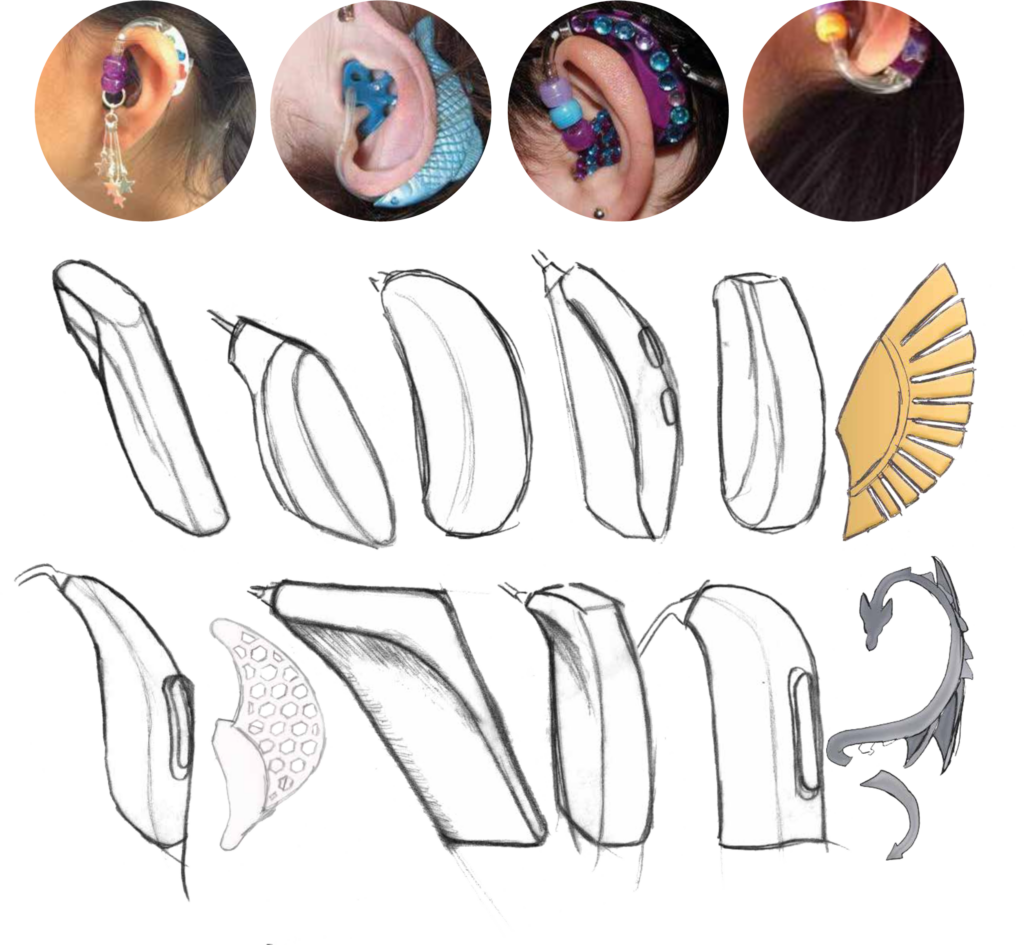
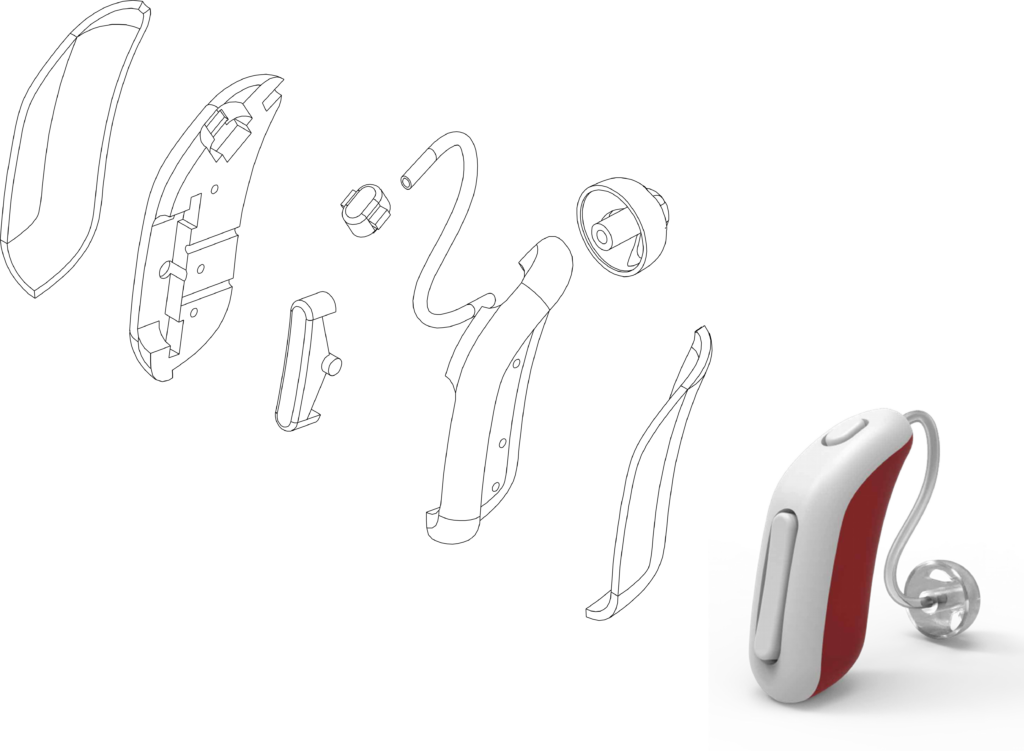
In our research on advanced functional materials, we developed a prototype using TCPoly’s proprietary 3D printable thermally conductive filaments, which exhibit a unique combination of high thermal conductivity and electrical insulation—properties that are critical for fabricating specialised and niche electrical components. These filaments, based on a modified polymer matrix infused with thermally conductive, non-metallic fillers, enable the additive manufacturing of complex geometries with integrated thermal management capabilities.
This is particularly advantageous in applications such as custom heat sinks, LED housings, and enclosures for sensitive electronic circuitry, where precise thermal dissipation is essential without risking electrical interference. Unlike traditional machining or casting, the use of TCPoly filament allows for rapid prototyping and on-demand production of components with embedded thermal pathways, all while maintaining dielectric integrity. Our findings suggest that incorporating this filament into small-scale production workflows can significantly streamline the development of compact, thermally-regulated electrical devices for aerospace, robotics, and advanced sensor systems.
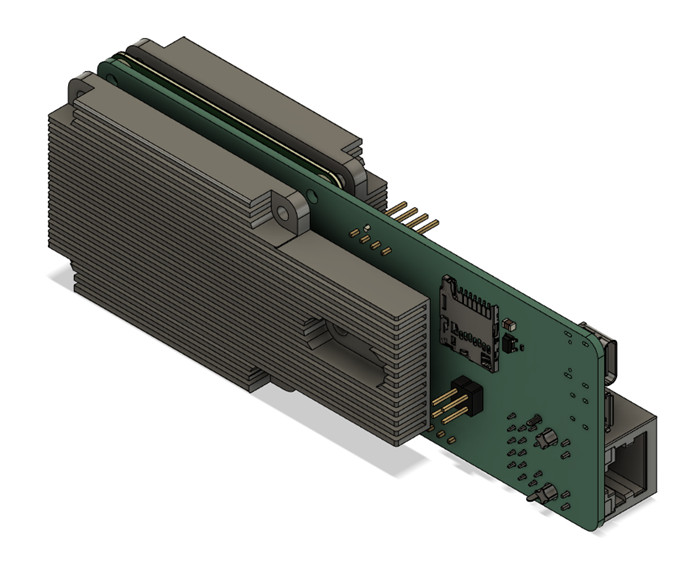
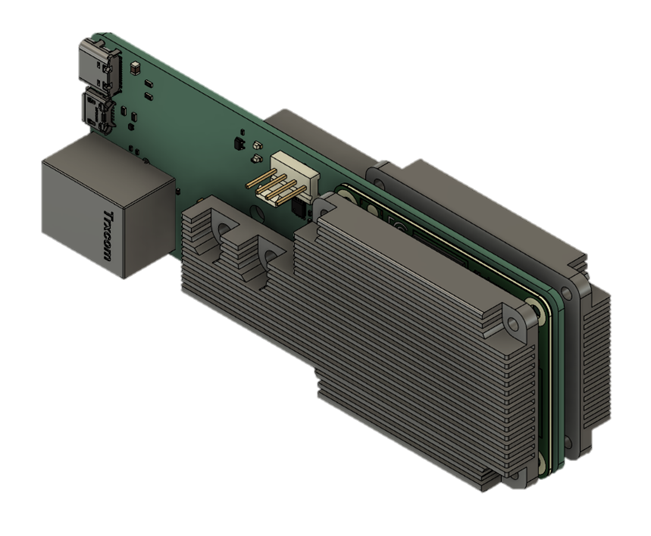
In our research on advanced manufacturing methods, we have developed rapid prototyping techniques for producing custom 3D enclosures for small-form-factor computers using on-site fused filament fabrication (FFF) 3D printers. By leveraging parametric CAD modelling and iterative design workflows, we enable the rapid development of enclosures optimised for thermal management, electromagnetic shielding, and component accessibility.
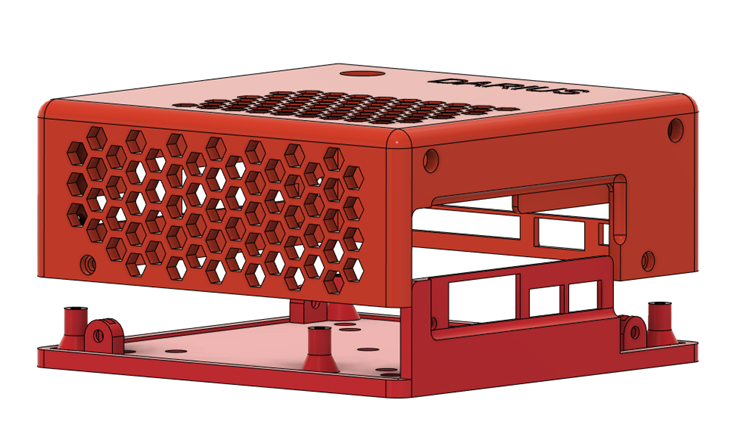
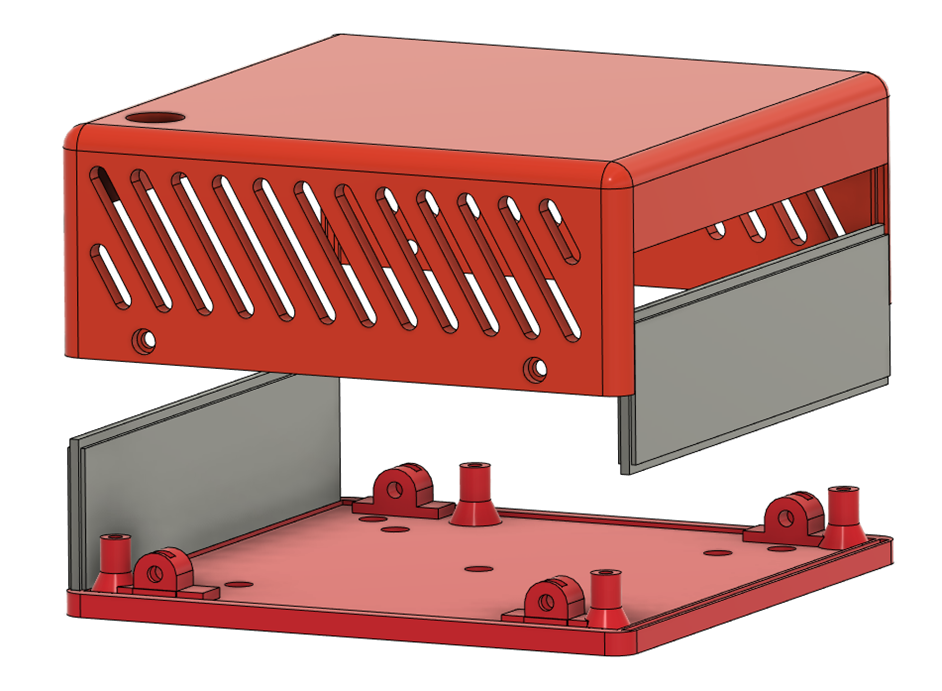
Using engineering-grade thermoplastics such as ABS, PETG, and PC blends, we can produce structurally robust housings tailored to the specific dimensions and port layouts of single-board computers (e.g., our own RapidAnalysis Xerxes Pi and Darius devices). The ability to fabricate enclosures on-site reduces lead times, minimises tooling costs, and allows for agile hardware development in research labs and field deployments.
Furthermore, integrating ventilation channels, snap-fit features, and mounting geometries into the print design enhances both functionality and assembly efficiency. This approach significantly accelerates the prototyping cycle for embedded computing applications in IoT, robotics, and edge computing environments.
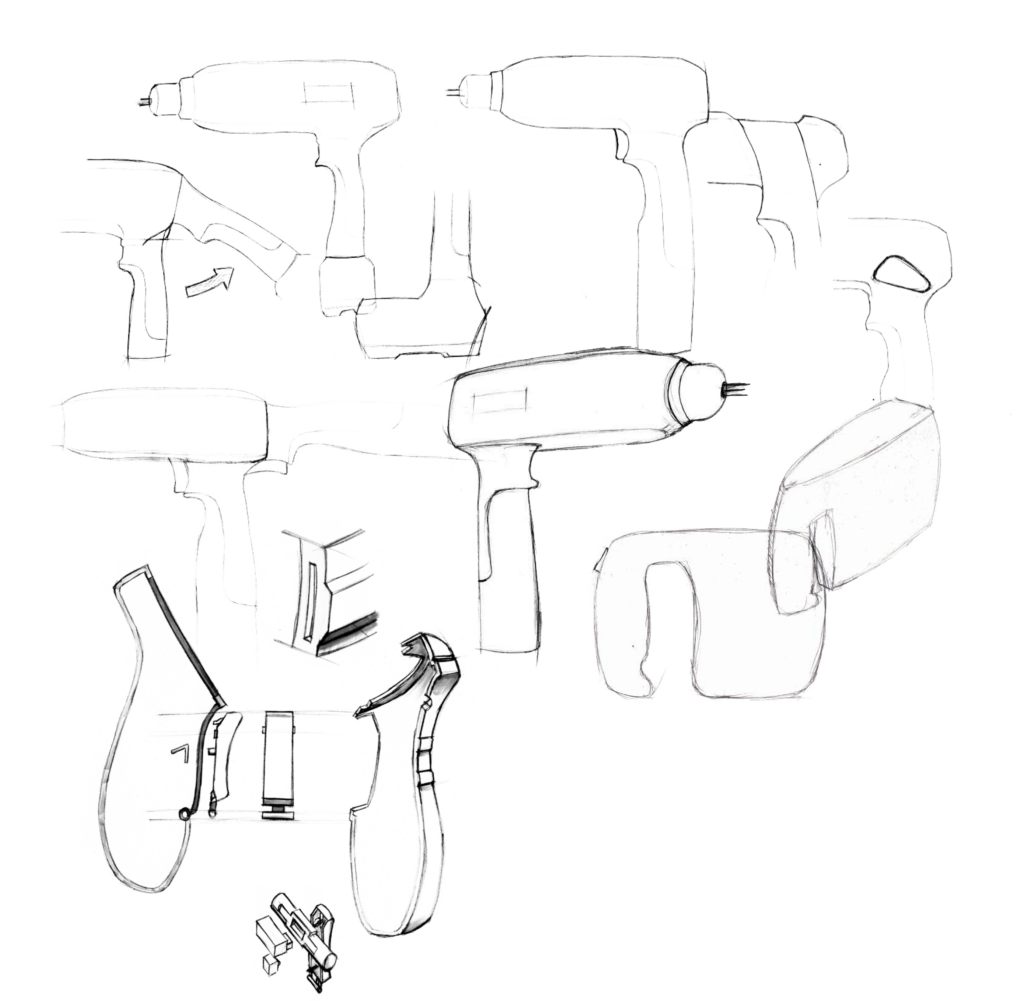

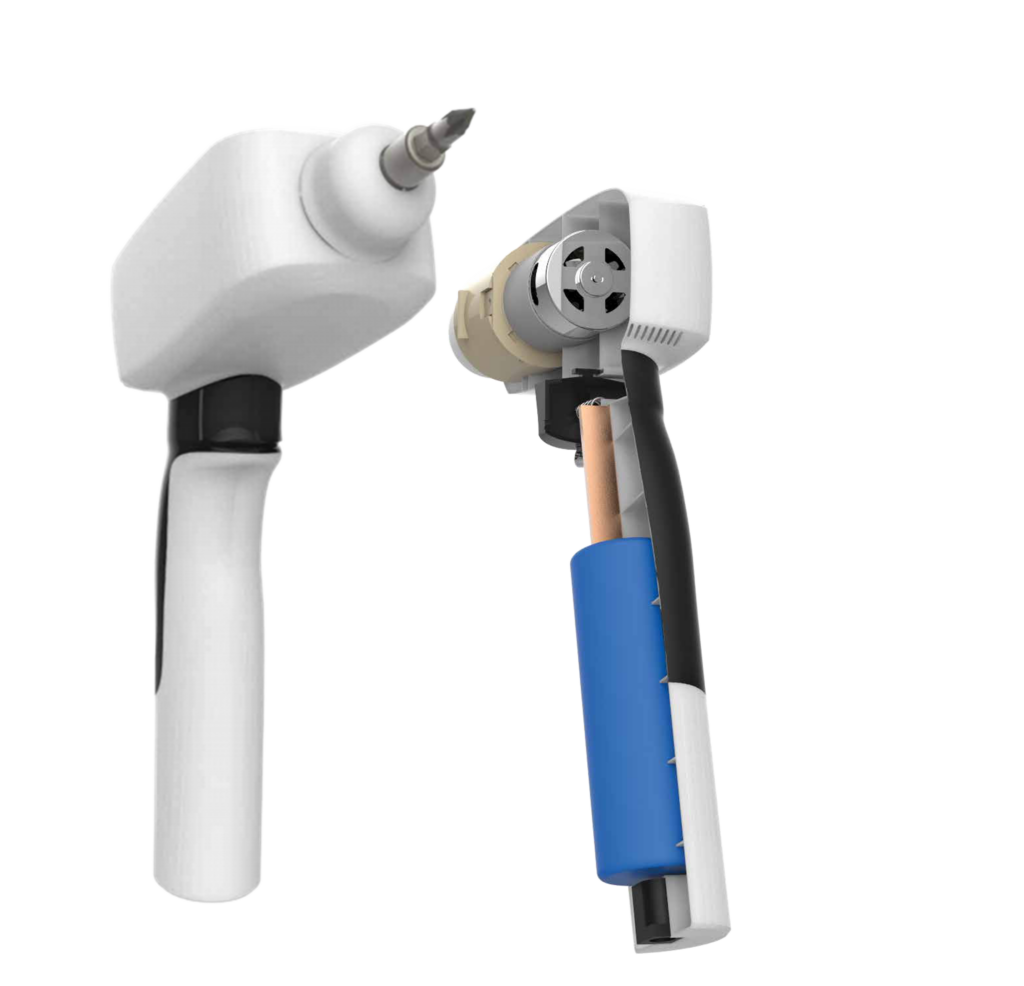
In our research on high-performance polymers for medical applications, we focused on the rapid prototyping of enclosures for surgical tools—specifically surgical drills—using on-site 3D printing technologies compatible with autoclave sterilisation. By employing high-temperature-resistant thermoplastics such as PEEK, PEKK, and ULTEM™ (PEI), we are able to fabricate precision housings that withstand repeated steam sterilization cycles at 121–134°C without degradation of mechanical integrity or dimensional stability.
These materials, processed through high-performance FFF or industrial SLS printers, enable the production of functional prototypes that can be evaluated under realistic surgical conditions. Rapid design iteration through CAD modeling and in-house printing allows for ergonomic optimization, integration of fluid ingress barriers, and alignment of internal component geometries, including drive shafts and control circuits.
On-site autoclaving facilitates immediate validation of thermal and structural resilience, significantly reducing development time for surgical-grade equipment. This workflow supports the agile development of novel surgical tools in hospital innovation labs, bridging the gap between concept and clinical readiness.
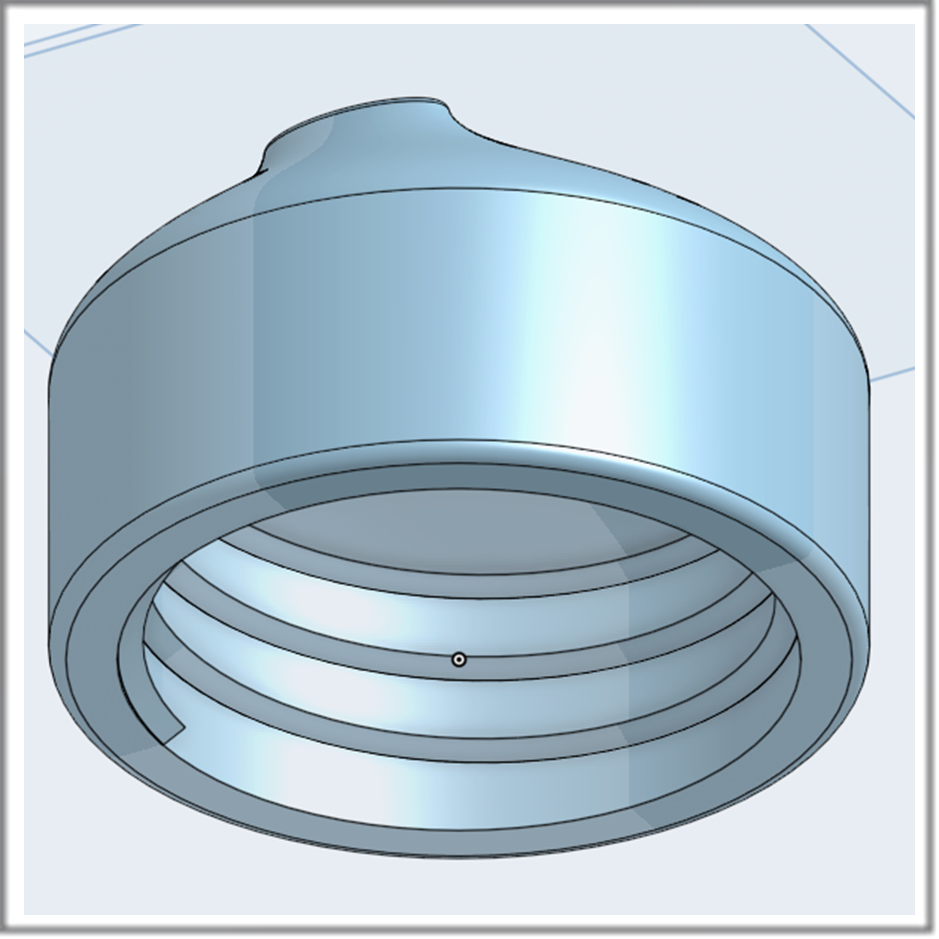
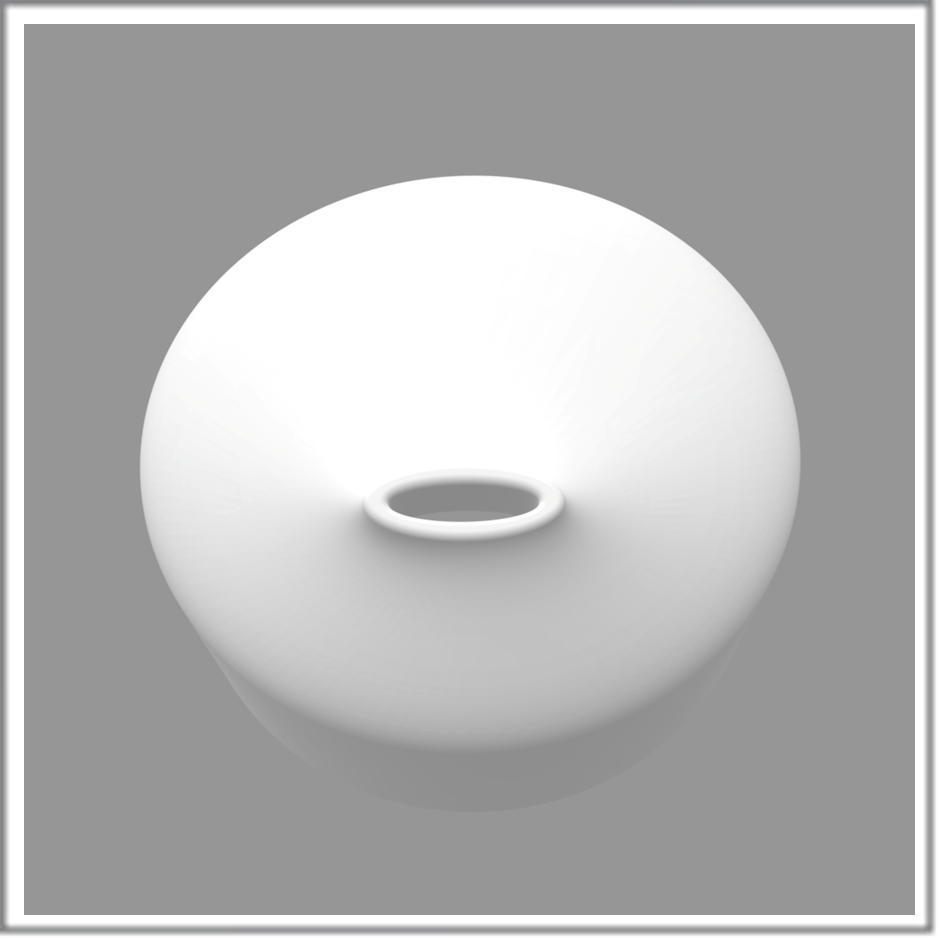

In our research on biomedical polymers and assistive infant feeding devices, we have proposed a design for a specialised baby bottle for infants with cleft palate conditions, incorporating features that address both anatomical challenges and clinical hygiene requirements. The design utilises medical-grade, high-temperature thermoplastics such as autoclavable silicone blends and polyetherimide (ULTEM™), chosen for their biocompatibility, chemical resistance, and ability to withstand repeated autoclave sterilisation cycles at 121–134°C. The bottle features a soft, pressure-sensitive valve-integrated nipple that regulates milk flow and compensates for the infant’s impaired suction, while an internal one-way diaphragm prevents air intake to reduce aspiration risk. CAD-driven design allows for precise control of flow channels and ergonomic shaping, which can be rapidly prototyped using in-house 3D printing and silicone casting techniques.
On-site autoclaving enables immediate validation of sterilisation compatibility, material resilience, and part integrity, accelerating iterative refinement and ensuring clinical readiness. This approach supports personalised, hygienic feeding solutions for infants with craniofacial anomalies, particularly in hospital settings or resource-constrained environments.
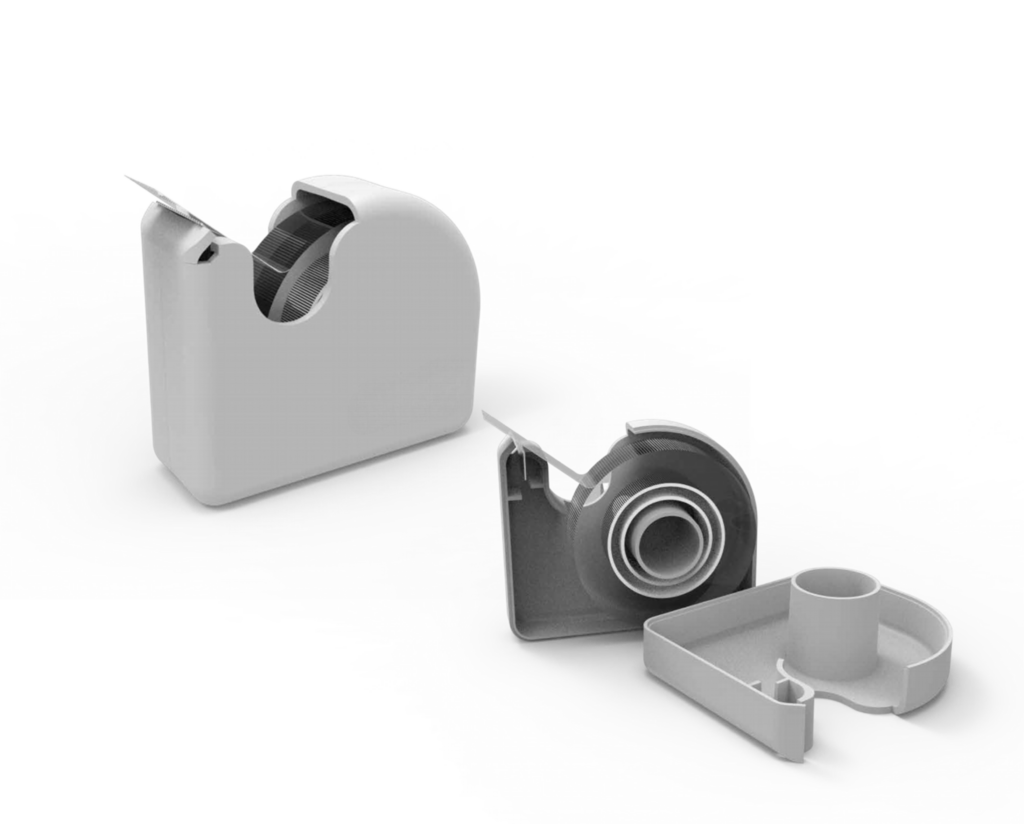
In our research on sterilisable medical-grade polymers and integrated surgical tools, we have proposed the design for an autoclave-ready magnetic surgical tape dispenser designed for use in sterile field environments. The device is fabricated using high-performance, autoclavable materials such as polyetherimide (ULTEM™) for the housing and surgical-grade stainless steel for the cutting blade, ensuring durability and dimensional stability through repeated autoclave cycles at 134°C.
The design incorporates embedded neodymium magnets, encapsulated within polymer barriers, allowing the dispenser to securely attach to stainless steel surgical trays without compromising sterilization integrity. Key features include a one-handed tear mechanism, a textured gripping surface for gloved use, and an open-frame geometry to facilitate thorough steam penetration during autoclaving.
Using precision additive manufacturing and CNC machining, the dispenser can be rapidly prototyped and tested on-site for mechanical performance and sterilization resilience. This device streamlines intraoperative workflow by providing secure, sterile access to surgical tape, reducing handling steps and minimizing contamination risk in critical care settings.